Porosity in Welding: Identifying Common Issues and Implementing Finest Practices for Avoidance
Porosity in welding is a prevalent issue that commonly goes undetected up until it causes considerable issues with the honesty of welds. In this discussion, we will discover the key elements adding to porosity formation, examine its damaging results on weld efficiency, and go over the ideal techniques that can be taken on to reduce porosity occurrence in welding procedures.
Common Reasons of Porosity
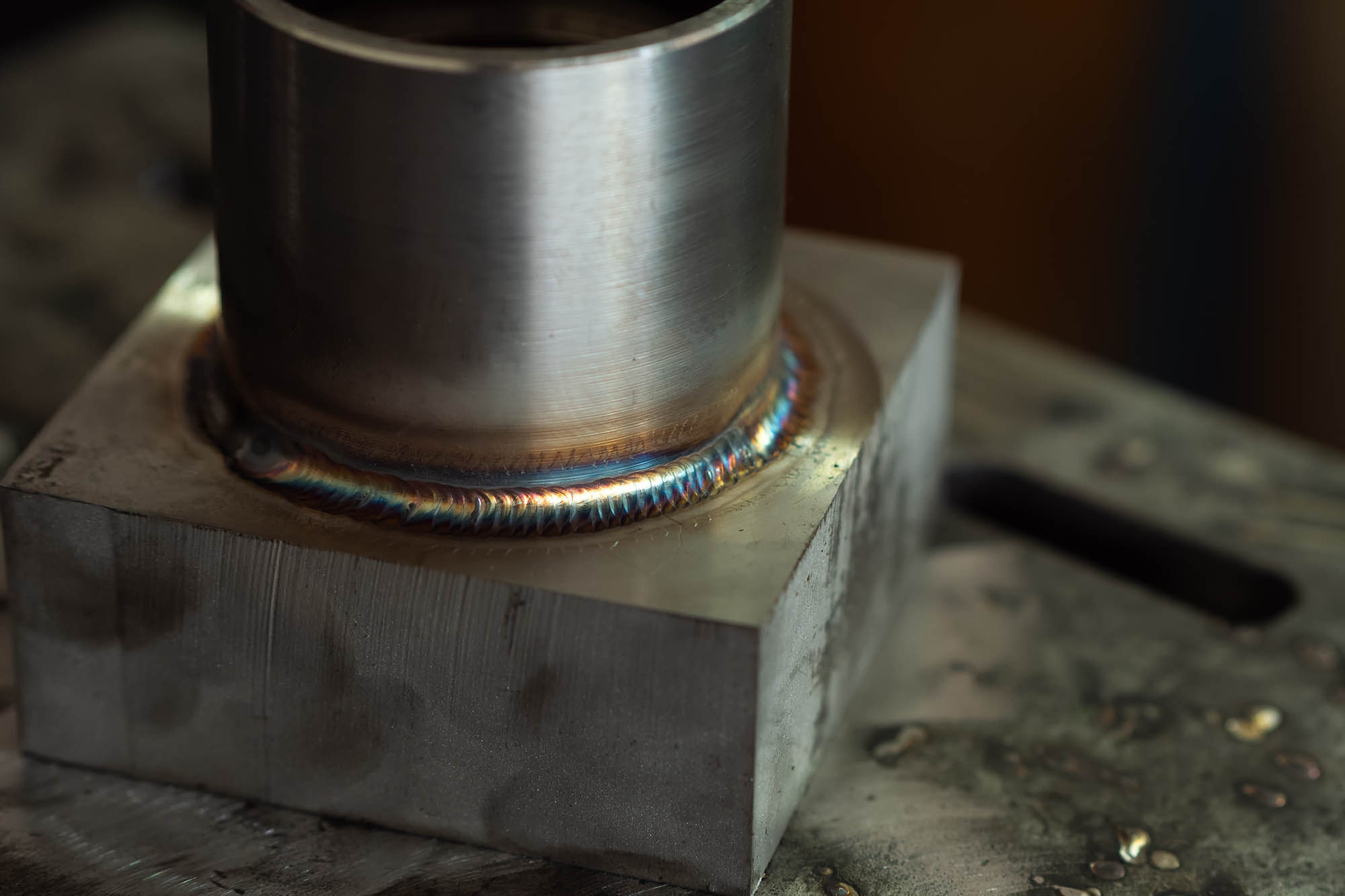
Making use of unclean or damp filler products can introduce impurities into the weld, contributing to porosity problems. To alleviate these typical reasons of porosity, detailed cleansing of base steels, correct securing gas selection, and adherence to optimum welding criteria are necessary practices in attaining high-grade, porosity-free welds.
Effect of Porosity on Weld High Quality

The visibility of porosity in welding can considerably jeopardize the structural honesty and mechanical properties of welded joints. Porosity produces voids within the weld steel, compromising its general strength and load-bearing ability.
Among the main effects of porosity is a decline in the weld's ductility and strength. Welds with high porosity levels often tend to display lower effect toughness and decreased capability to deform plastically prior to fracturing. This can be particularly worrying in applications where the welded parts undergo vibrant or cyclic loading conditions. Additionally, porosity can hamper the weld's ability to successfully send forces, leading to premature weld failure and possible security hazards in critical structures.
Best Practices for Porosity Avoidance
To boost the architectural stability and top quality of welded joints, what specific measures can be carried out to decrease the event of porosity throughout the welding procedure? Using the appropriate welding strategy for the certain material being web bonded, such as readjusting the welding angle and weapon position, can further stop porosity. Routine inspection of welds and prompt removal of any concerns determined throughout the welding procedure are important techniques to read the full info here prevent porosity and create high-quality welds.
Importance of Correct Welding Techniques
Carrying out correct welding strategies is critical in making certain the architectural honesty and top quality of bonded joints, building upon the foundation of efficient porosity avoidance measures. Welding strategies directly affect the general toughness and resilience of the bonded framework. One essential element of correct welding strategies is maintaining the appropriate warmth input. Extreme heat can cause raised porosity as a result of the entrapment of gases in the weld swimming pool. Conversely, inadequate warmth might result in incomplete blend, developing possible weak factors in the joint. Additionally, utilizing the proper welding specifications, such as voltage, current, and travel rate, is critical for attaining audio welds with minimal porosity.
Furthermore, the choice of welding procedure, whether it be MIG, TIG, or stick welding, ought to straighten with the specific demands of the project to guarantee optimum results. Appropriate cleansing and preparation of the base metal, along with choosing the ideal filler product, are additionally necessary components of skillful welding strategies. By adhering to these finest methods, welders can reduce the danger of porosity development and create premium, structurally sound welds.

Evaluating and Quality Assurance Steps
Quality control steps play a vital duty in validating the integrity and integrity of bonded joints. Testing procedures are crucial to detect and stop porosity in find out welding, ensuring the strength and longevity of the final product. Non-destructive screening techniques such as ultrasonic testing, radiographic screening, and visual evaluation are generally used to recognize prospective defects like porosity. These methods allow for the evaluation of weld top quality without compromising the honesty of the joint. What is Porosity.
Post-weld examinations, on the various other hand, examine the final weld for any defects, consisting of porosity, and confirm that it meets defined standards. Executing a comprehensive top quality control strategy that consists of thorough screening procedures and examinations is paramount to decreasing porosity concerns and guaranteeing the overall top quality of welded joints.
Conclusion
In conclusion, porosity in welding can be a typical issue that affects the high quality of welds. By identifying the usual reasons for porosity and executing best practices for avoidance, such as appropriate welding techniques and screening procedures, welders can make certain premium quality and dependable welds. It is necessary to prioritize avoidance techniques to minimize the event of porosity and preserve the honesty of bonded structures.